Lancing Wire GI-SS
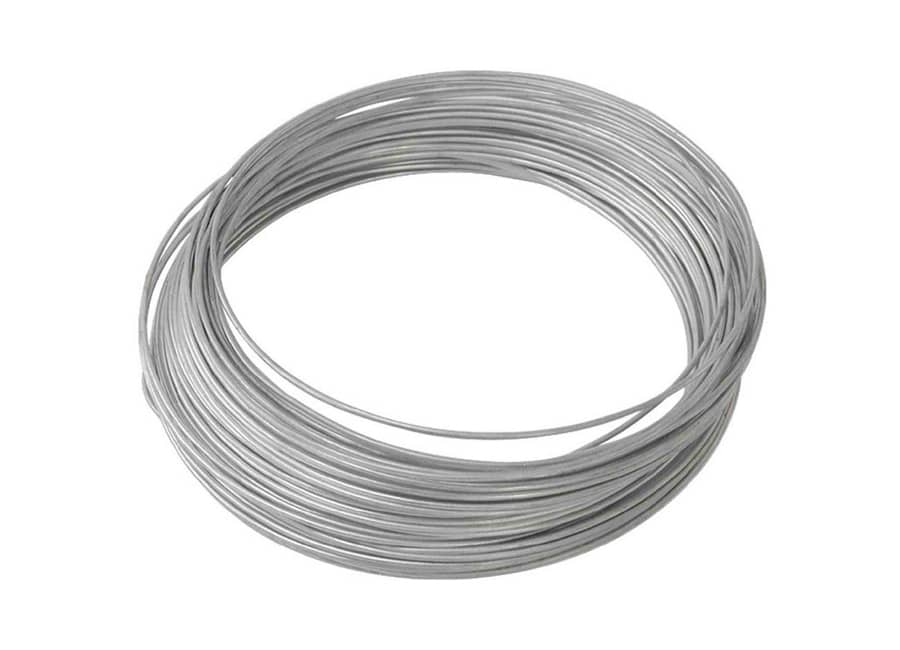
Lancing wire, available in galvanized iron (GI) and stainless steel (SS) variants, is a specialized tool used primarily in the steelmaking industry for oxygen lancing applications.
Key Features
Our Rockwool Slab Insulation excels in thermal performance, effectively minimizing heat transfer. This feature contributes to energy conservation, reduced utility costs, and the creation of comfortable indoor environments.
Lancing wire is available in various diameters and lengths, depending on the specific application and requirements of the steelmaking process. Common diameters range from a few millimeters to several centimeters, while lengths can vary from a few meters to tens of meters.
Lancing wire GI-SS is primarily used for oxygen lancing, a process employed in steelmaking and metallurgy for cutting, piercing, or melting metal alloys, particularly in the refining of molten metal in blast furnaces, converters, ladles, and other metallurgical vessels. The lancing wire serves as a conduit for delivering a high-pressure stream of oxygen into the molten metal, initiating exothermic reactions that facilitate various metallurgical processes.
Lancing wire GI-SS is designed to withstand high temperatures generated during the oxygen lancing process. Both galvanized iron and stainless steel variants exhibit excellent heat resistance, ensuring durability and reliability under extreme operating conditions.
Lancing wire GI-SS possesses a balance of flexibility and strength, allowing it to be easily manipulated and maneuvered into position for precise lancing operations. The wire must withstand the mechanical stresses associated with the insertion and manipulation process without breaking or deforming.
While galvanized iron lancing wire offers good corrosion resistance due to its zinc coating, stainless steel lancing wire provides superior resistance to corrosion and oxidation, making it suitable for use in corrosive environments or prolonged exposure to high temperatures.
Proper handling and safety precautions are essential when working with lancing wire GI-SS due to the inherent risks associated with oxygen lancing processes, including high temperatures, molten metal splatter, and potential release of hazardous gases. Operators should receive adequate training and use appropriate personal protective equipment to minimize the risk of accidents or injuries.
Applications

Residential
Buildings

Commercial
Structures

Industrial
Facilities

Educational
Institutions

Healthcare
Facilities
GI Wire Netting
Galvanized iron (GI) wire netting is a versatile and widely used material in construction, agriculture, fencing, and other applications where a durable and corrosion-resistant mesh is required.
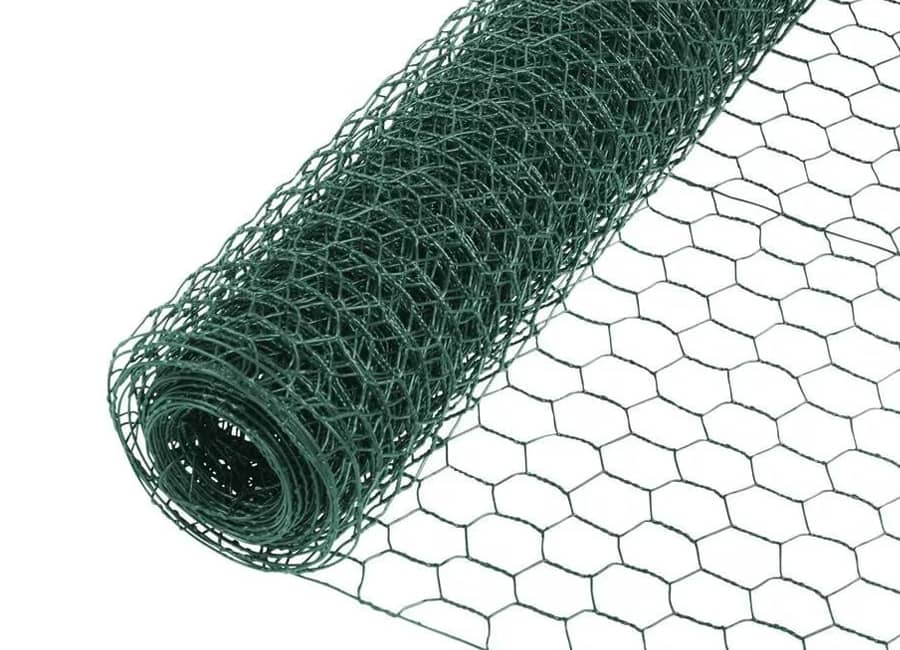
Key Features
GI wire netting is typically made from high-quality steel wire that has been coated with a layer of zinc through a process called galvanization. This zinc coating provides excellent corrosion resistance, making the wire netting suitable for outdoor use and exposure to moisture and harsh weather conditions.
GI wire netting is available in various mesh sizes and wire gauges to suit different applications. The mesh size refers to the spacing between adjacent wires in the netting, while the wire gauge indicates the thickness or diameter of the wire. Common mesh sizes range from small, fine meshes used for insect screening to larger meshes used for fencing and construction reinforcement.
Galvanized iron wire netting is known for its strength and durability. The galvanization process enhances the wire’s resistance to corrosion, rust, and mechanical damage, ensuring a long service life even in harsh environments. This makes it ideal for applications requiring sturdy and reliable mesh, such as fencing, animal enclosures, and construction reinforcement.
GI wire netting is a versatile material with a wide range of applications. It can be used for fencing to enclose gardens, agricultural fields, livestock, and poultry farms. It is also used for screening windows and doors to keep out insects while allowing airflow. Additionally, GI wire netting is employed in construction as reinforcement for plastering, concrete, and masonry work to improve structural strength and prevent cracking.
GI wire netting is easy to install and can be cut to size using simple tools like wire cutters or shears. It can be attached to existing structures or supports using nails, staples, or wire ties. For fencing applications, it can be stretched between posts or attached to wooden or metal frames to create a secure enclosure.
Compared to other materials like stainless steel or aluminum, galvanized iron wire netting is often more cost-effective while still providing excellent corrosion resistance and durability. This makes it a popular choice for budget-conscious projects without compromising on quality or performance.
While GI wire netting is highly resistant to corrosion, periodic maintenance may be required to remove dirt, debris, or vegetation that can accumulate on the surface over time. Regular inspections and cleaning can help prolong the lifespan of the netting and ensure optimal performance.
Applications

Industrial
Processes

HVAC (Heating, Ventilation, and Air Conditioning) Systems

Commercial
Building Insulation

Residential
Construction

Equipment
Insulation
GI Wild Mesh
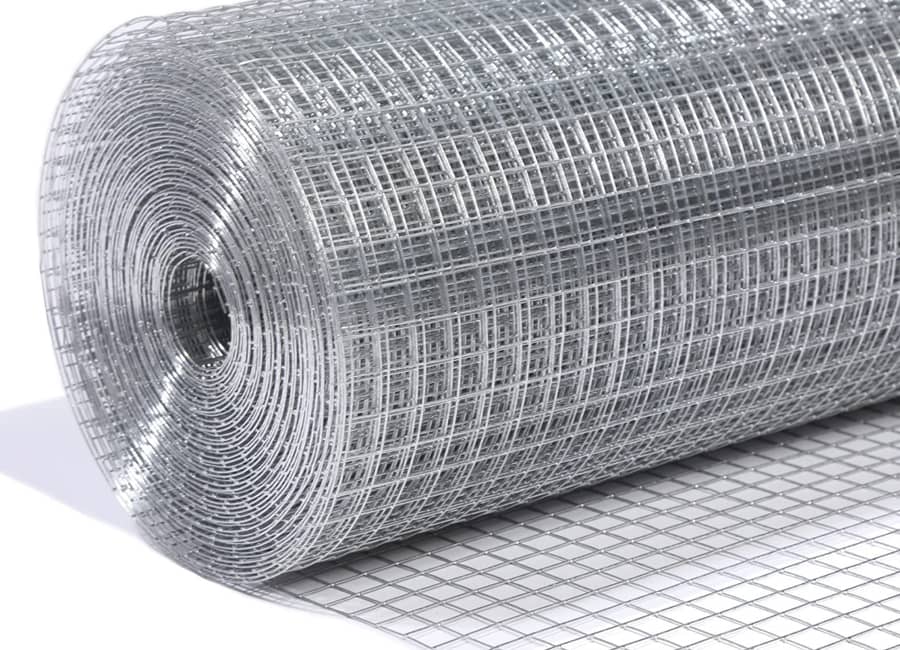
GI wild mesh, also known as galvanized iron wild mesh, is a type of wire mesh commonly used in agricultural and horticultural applications to protect crops and plants from wild animals and pests.
Key Features
GI wild mesh is typically made from galvanized iron wire, which is steel wire coated with a layer of zinc through the process of galvanization. This zinc coating provides excellent corrosion resistance, making the mesh suitable for outdoor use and exposure to harsh weather conditions.
GI wild mesh comes in various mesh sizes and wire gauges to suit different applications and levels of protection. The mesh size refers to the spacing between adjacent wires in the mesh, while the wire gauge indicates the thickness or diameter of the wire. Common mesh sizes range from small, fine meshes to larger meshes, depending on the type of crops and the size of the pests being targeted.
GI wild mesh serves as a physical barrier to prevent wild animals, birds, and pests from accessing crops and plants. It can be installed as fencing around agricultural fields, orchards, vineyards, and garden plots to deter animals from damaging or eating the produce. The sturdy construction of the mesh provides reliable protection against larger animals such as deer, rabbits, and birds.
In addition to protecting crops from wildlife, GI wild mesh has other uses in agriculture and horticulture. It can be used to create trellises for supporting climbing plants such as tomatoes, beans, and cucumbers. The mesh can also be employed as a barrier to prevent soil erosion or to support netting for shade or frost protection.
GI wild mesh is relatively easy to install and can be cut to size using simple tools such as wire cutters or shears. It can be attached to existing structures or posts using nails, staples, or wire ties. For larger installations, it can be stretched between posts or attached to wooden or metal frames to create a secure perimeter.
The galvanized iron construction of the mesh provides excellent durability and resistance to rust and corrosion, ensuring a long service life even in harsh outdoor environments. This makes GI wild mesh a cost-effective solution for long-term crop protection.
While GI wild mesh requires minimal maintenance, periodic inspections may be necessary to ensure that the mesh remains intact and properly secured. Any damage or areas of weakness should be repaired promptly to maintain the effectiveness of the mesh as a barrier against wildlife.
Applications

Industrial Piping Systems

HVAC (Heating, Ventilation, and Air Conditioning) Systems

Process Piping in Manufacturing

Commercial Building Pipework

Residential Plumbing Systems
Sheet Metal Screw
Sheet metal screws, also known as self-tapping screws, are specialized fasteners designed for securely joining sheet metal or thin materials together.
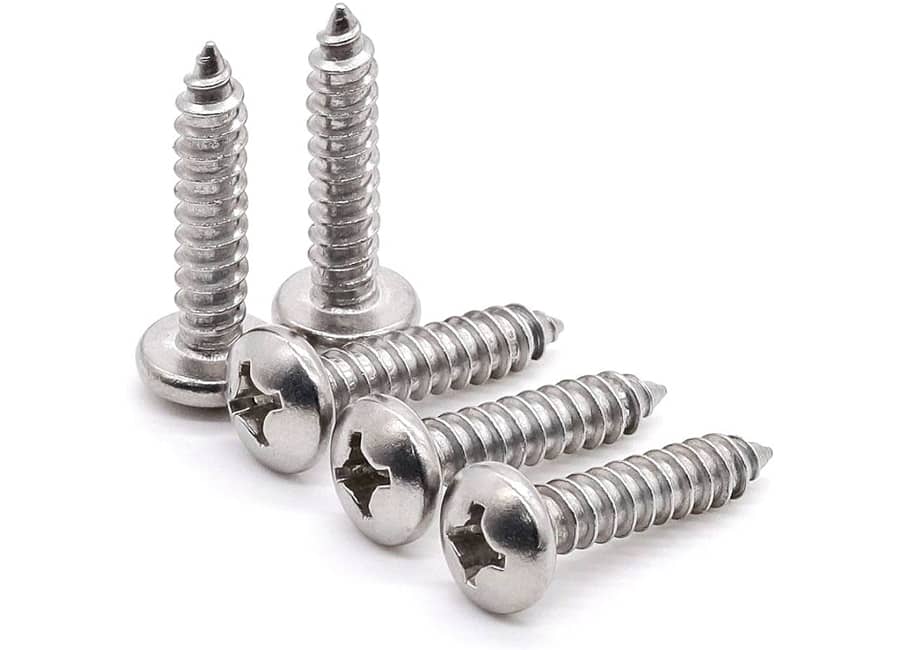
Key Features
Sheet metal screws feature sharp, angled threads that are designed to cut into and grip the material they are being driven into. These threads allow the screw to create its own mating threads in the metal, eliminating the need for pre-drilled holes or tapping threads.
Sheet metal screws typically come with various point styles to suit different applications:
- Self-Drilling (Tek) Point: These screws have a drill-like point that can penetrate the metal without the need for a pre-drilled hole.
- Self-Tapping (Type A) Point: These screws have a sharp, tapered point that can cut its own threads in the metal as it is driven.
- Type AB Point: Combines features of both self-drilling and self-tapping points, making it suitable for a wide range of materials.
Sheet metal screws come with different head types, including:
- Pan Head: Rounded, low-profile head that offers a wide bearing surface and is suitable for applications where a flush finish is desired.
- Flat Head (Countersunk): Head sits flush with the surface of the material when fully installed, providing a smooth finish.
- Hex Head: Head is shaped like a hexagon, allowing for increased torque during installation and providing a more secure fastening.
Sheet metal screws are commonly made from steel, stainless steel, or other corrosion-resistant materials. They may also feature various coatings or platings such as zinc, nickel, or chrome to enhance corrosion resistance and provide a more attractive appearance.
Sheet metal screws are used in a wide range of applications where joining thin materials, particularly sheet metal, is required. Common applications include:
- HVAC (Heating, Ventilation, and Air Conditioning) systems
- Automotive assembly and repair
- Metal roofing and siding installation
- Electrical and electronics enclosures
- Furniture assembly
- Sheet metal fabrication and construction projects
Sheet metal screws are typically installed using a power screwdriver or drill with a suitable screwdriver bit. The screws should be driven straight into the material at a controlled speed to prevent stripping or damaging the threads. Proper torque should be applied to ensure a secure and tight fastening.
Applications

Attic
Insulation

Wall Cavity
Insulation

Floor
Insulation

Soundproofing
Applications

Commercial & Industrial Spaces
Aluminium SS Bands
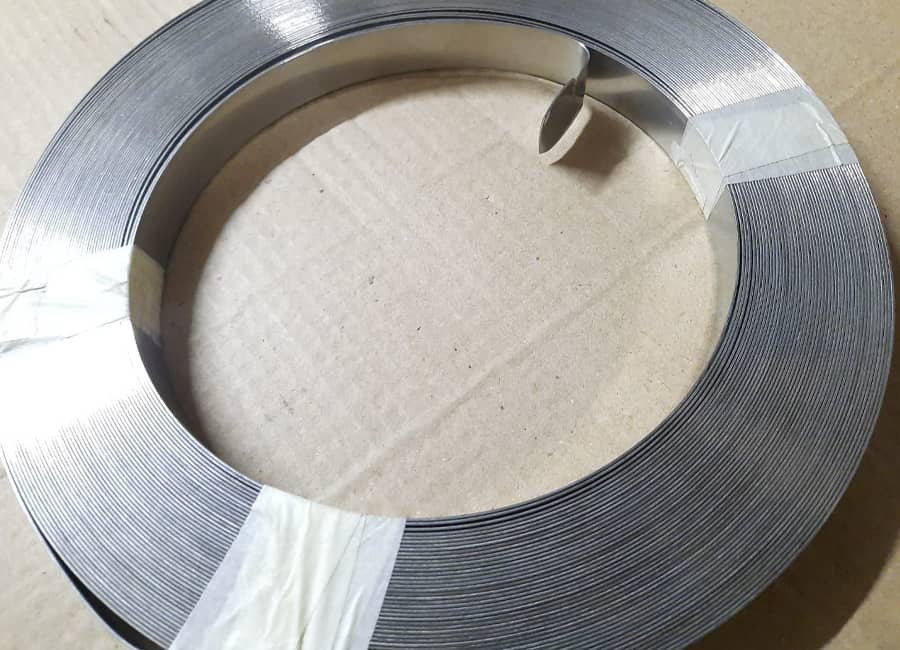
Aluminum and stainless steel bands are occasionally utilized as components in insulation systems, albeit in specialized applications. When used in insulation, these bands typically serve as fasteners or support elements rather than the primary insulating material.
Key Features
Aluminum and stainless steel bands can be employed as part of a fastening system for securing insulation materials in place. They are often wrapped around insulation blankets, mats, or jackets to hold them snugly against pipes, ducts, tanks, or other surfaces.
In some insulation applications, aluminum and stainless steel bands may serve as a support structure for holding insulation materials in position. They can be used to create framework or strapping systems that support the weight of insulation and prevent sagging or displacement over time.
One of the advantages of using aluminum and stainless steel bands in insulation applications is their corrosion resistance. These materials are not susceptible to rust or degradation, making them suitable for use in environments where moisture or chemical exposure may be a concern.
Aluminum and stainless steel bands can withstand a wide range of temperatures, making them suitable for use in both hot and cold insulation applications. They maintain their structural integrity and strength even under extreme temperature conditions.
Aluminum and stainless steel bands offer versatility in insulation applications due to their flexibility, strength, and compatibility with various insulation materials. They can be easily customized and adapted to fit different shapes, sizes, and configurations.
Crafted from high-quality and durable mineral wool fibers, our building roll insulation is resistant to moisture, mold, and pests. This ensures longevity and consistent performance, making it a reliable choice for enhancing the overall durability of structures.
Applications

Residential Wall and Ceiling Insulation

Commercial Building Insulation

Industrial Applications

HVAC Duct Insulation

Soundproofing Projects
Insulation Pins
Insulation pins, also known as insulation hangers or weld pins, are essential components used in insulation systems to secure insulation materials to surfaces, such as metal ductwork, pipes, tanks, or equipment.
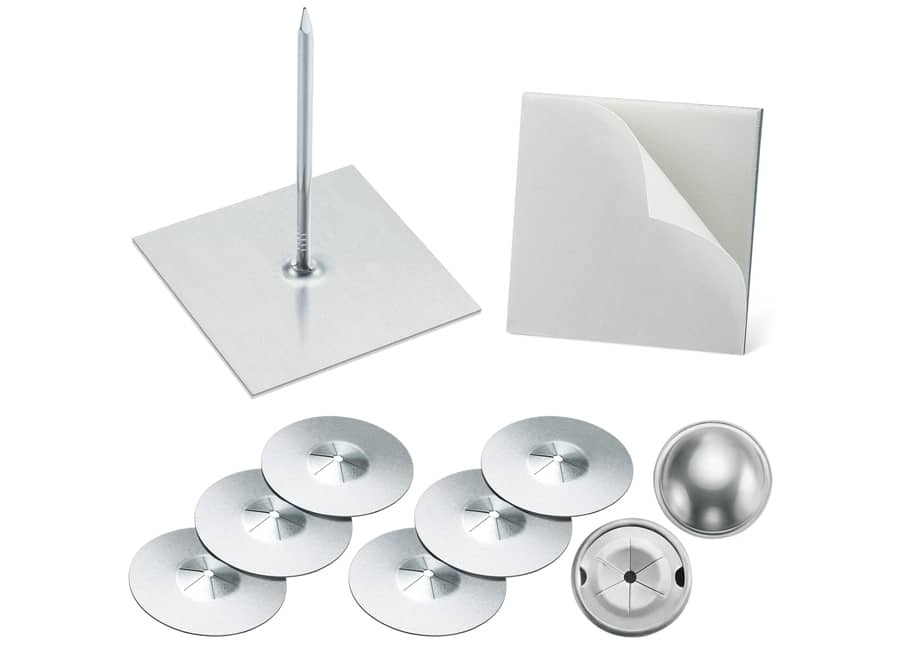
Key Features
Insulation pins are typically made from corrosion-resistant materials such as stainless steel, galvanized steel, or aluminum. They consist of a straight or twisted metal shaft with a flat or domed head at one end and a pointed tip at the other.
Insulation pins come in various types to suit different applications and installation methods. Common types include:
- Weld Pins: These pins are welded directly onto the surface of the substrate using a stud welding process. They provide a permanent and secure attachment for insulation materials.
- Self-Adhesive Pins: These pins feature a self-adhesive base that allows for quick and easy installation without the need for welding. They are suitable for use on smooth, clean surfaces where welding may not be feasible.
- Stick Pins: These pins have a pointed tip at one end and a flat or domed head at the other. They are inserted through the insulation material and then mechanically fastened to the substrate using a washer or locking cap.
- Perforated Base Pins: These pins feature a perforated base that allows for mechanical fastening to the substrate using screws or nails. They provide a strong and durable attachment for insulation materials.
Insulation pins are available in various lengths and diameters to accommodate different thicknesses of insulation materials and substrate types. The length of the pin should be sufficient to penetrate through the insulation material and securely anchor it to the substrate.
Insulation pins are installed at regular intervals across the surface of the substrate to ensure uniform support and attachment of the insulation material. The pins are typically spaced according to the specifications provided by the insulation manufacturer. Installation methods may include welding, adhesive bonding, or mechanical fastening, depending on the type of pin and substrate.
Insulation pins play a crucial role in maintaining the integrity and effectiveness of insulation systems by preventing the displacement or movement of insulation materials. They help reduce heat loss or gain, control condensation, and improve energy efficiency in a wide range of industrial, commercial, and residential applications.
Applications

Attic
Insulation

Wall Cavity
Insulation

Floor
Insulation

Soundproofing
Applications

Commercial & Industrial Spaces
Connect with us for tailored insulation solutions that redefine comfort.
Click ‘Get in Touch’ and let’s elevate your space together.